超声波雾化喷涂技术在燃料电池中的应用优势显著,尤其在提升催化剂利用效率、优化涂层均匀性、降低生产成本等方面表现突出。以下结合技术原理与行业实践,详细阐述其核心优势:
一、高材料利用率与成本控制
1.减少贵金属催化剂浪费
传统喷涂方法(如空气喷涂)因高压气体导致涂料反弹和飞溅,材料利用率仅20%-30%,而超声波喷涂通过高频振动雾化液体,无需高压气体,材料利用率可达90%以上,显著降低铂、铱等贵金属的消耗。例如,在质子交换膜燃料电池(PEMFC)中,铂催化剂的利用率从传统方法的50%提升至90%,材料成本降低50%。
2.纳米级精准控制
通过调节超声波频率,雾化液滴粒径可控制在10μm-50μm,甚至达到纳米级精度(如数十纳米),实现超薄涂层(5-15微米)的均匀沉积,减少材料冗余。
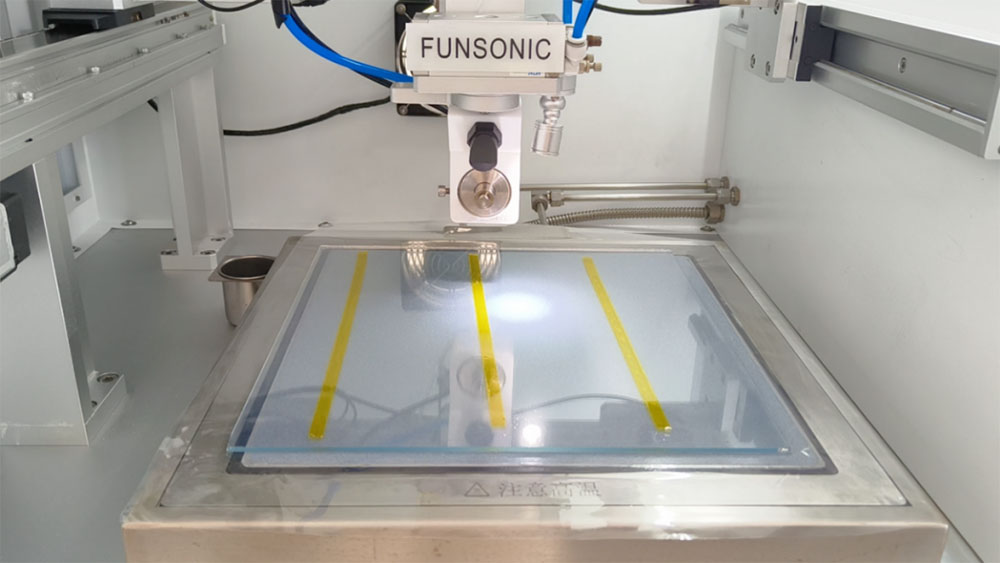
二、涂层均匀性与电极性能提升
1.避免催化剂团聚
超声波振动在雾化过程中同步分散催化剂悬浮液中的颗粒,打破团聚现象,形成多孔且致密的催化层结构,增加比表面积,提升电化学反应活性。例如,碳黑与铂基催化剂的分散均匀性提高后,电极的电流密度和耐久性均显著增强。
2.复杂表面适应性
超声波喷涂适用于气体扩散层的碳纸、质子交换膜等微观粗糙表面,通过真空吸附和加热平台保持膜材料平整,避免喷涂过程中的溶胀或变形,确保涂层与基材结合力强。
三、工艺自动化与规模化生产
1.高效量产能力
多喷嘴阵列设计支持宽幅喷涂,例如FUNSONIC钙钛矿专用超声波喷涂设备,整台设备采用15个喷头集成,可实现24小时不间断喷涂生产,自动化三轴运动系统,提升生产效率并减少人工干预。
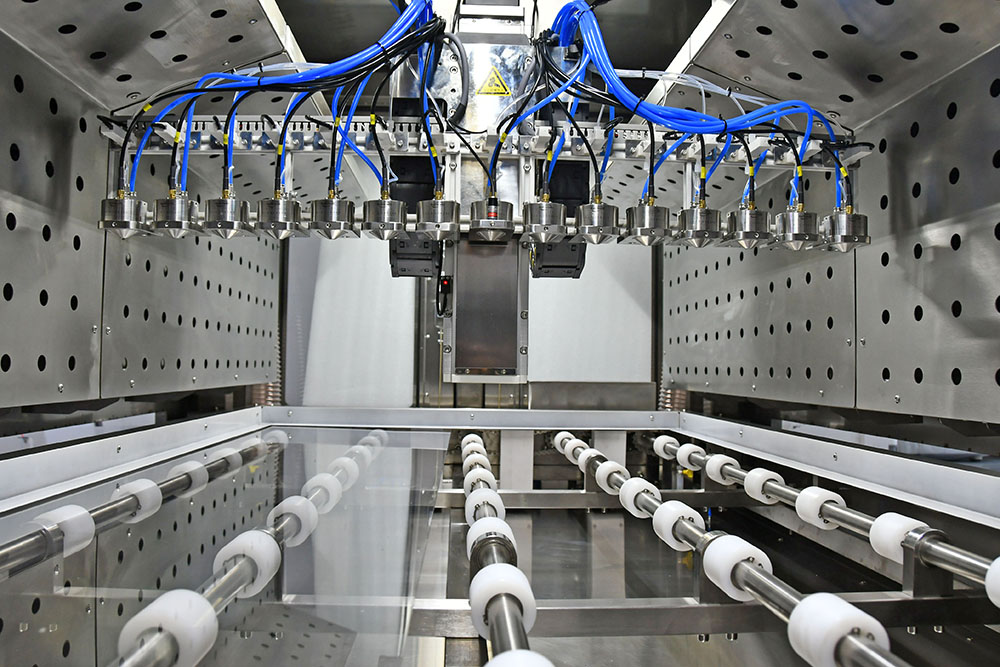
2.参数精准可控
喷涂速率、基底温度、移动路径、喷涂尺寸等参数均通过电脑PLC系统设置精准调控;确保涂层厚度误差小于5%,负载量一致性高。
四、环保与可持续性
1.低污染、低损耗
超声波喷涂仅利用少量有机溶剂(稀释剂)的辅助,工艺过程可大大减少挥发性有机物(VOC)排放。喷涂方式采用非接触式喷涂工艺技术,有效避免了外载器具对基膜材料表面的物理损伤,同样也延长喷头组件使用寿命。
2.节能特性
相较于传统高温溅射或化学气相沉积(CVD),超声波喷涂在常温或低温条件下即可完成,能耗降低30%-50%。
五、总结
超声波雾化喷涂技术通过高精度雾化、材料高效利用、工艺自动化等优势,成为燃料电池产业降本增效的核心工艺。其在膜电极组件(MEA)等关键组件的应用不仅提升了电池性能,还为氢能产业的规模化与可持续发展提供了技术保障。
FUNSONI现为客户朋友提供免费的打样服务,联系客服即可参与活动。